
KVT-Beschichtungsverfahren
Für jede Anwendung das richtige Verfahren
Das thermische Spritzen ist eine erprobte und nachweislich erfolgreiche Technologie. Seit über 100 Jahren ist diese Technologie in nahezu allen Industriezweigen im Einsatz.
Auf das Verfahren wird zurückgegriffen, um auf eine Metalloberfläche Schichten aufzutragen, die Bauteile gegen Verschleiß, Korrosion oder Temperatur oder kombinierte Angriffsarten schützt. In allen thermischen Spritzprozessen werden kleine Partikel des Beschichtungswerkstoffes in einer Spritzpistole aufgeheizt und beschleunigt sowie im Weiteren auf die zu beschichtende Substratoberfläche gespritzt. Wenn die Temperatur und die Geschwindigkeit der Partikel hoch genug ist, formen diese eine Schicht mit den gewünschten Eigenschaften und der erforderlichen Haftfestigkeit zum Untergrund.
Der Vorteil des thermischen Spritzens ist, dass durch die Kombination von Grundwerkstoffen und die hohe Anzahl an Spritzzusätzen im Regelfall fast immer eine ideale Lösung für einen Verschleißschutz gefunden werden kann. Die Wahl des Schichtsystems wird dabei auch beeinflusst durch die Beschichtungsverfahren.
Mithilfe expandierender Verbrennungsgase wird ein pulverförmiger Spritzzusatz in einer Acetylen-Sauerstoff-Flamme auf die vorbereitete Werkstückoberfläche an- oder aufgeschmolzen. Ergänzend kann – falls notwendig – zur Beschleunigung der Pulverteilchen ein zusätzliches Gas wie Argon oder Stickstoff verwendet werden.
Bei den Pulvern wird zwischen selbstfließenden und selbsthaftenden unterschieden. Grundsätzlich benötigen die selbstfließenden Pulver eine thermische Nachbehandlung. Dieser „Einschmelz-Prozess“ erfolgt überwiegend durch Acetylen-Sauerstoff-Brenner.
Vorteile:
- Hohe Vielfalt an Spritzwerkstoffen
- Das Schichtsystem ist gas- und flüssigkeitsdicht
- Porenfreie Schichten
- Gute Verschleißbeständigkeit bei linearer, punktueller und Flächenbelastung
- Sehr hohe Haftfestigkeit
- Metallurgische Verbindung zum Grundwerkstoff
- Sehr gute Nachbearbeitung der Schicht durch Drehen, Fräsen, Schleifen und Läppen
- Gute Korrosionsbeständigkeit gegen Laugen, schwache Säuren sowie wässrige Lösungen
Nachteile:
- Kann nicht partiell aufgetragen werden
- Chromstähle sind zum Schmelzverbund nicht geeignet
- Hohe Temperaturbelastung des Grundwerkstoffes
- Eingeschränkte Bauteilgeometrie
Schichtstärke: 0,3–0,8 mm
Schichthaftung: gut durch Diffusion
Temperaturbelastung: sehr hoch, bis zu 1150 °C
Grundwerkstoffe: CrNi- / Duplex-Stahl, Ni-Basis-Legierung
Bearbeitung: drehen, schleifen, läppen der Schichten möglich
Im Vergleich zum Flammspritzen wird beim HVOF das beschleunigte Prozessgas auf Überschallgeschwindigkeit (>2000 m/s) gebracht. In oder nach der Brennkammer wird ein pulverförmiger Spritzzusatz zugeführt. Die Gasverbrennung ist kontinuierlich und erfolgt mit hohen Drücken innerhalb der Brennkammer. Der in der Brennkammer erzeugte hohe Druck des Brenngas-Sauerstoff-Gemisches und die nachgeordnete Expansionsdüse erzeugen eine hohe Strömungsgeschwindigkeit im Gasstrahl, bedingt dadurch werden die Spritzpartikel auf eine hohe Partikelgeschwindigkeit beschleunigt. Die Partikelgeschwindigkeit beträgt bis zu 800 m/s.
Vorteile:
- Geringe thermische Belastung des Grundwerkstoffes
- Hohe Schichthärten sind erzielbar
- Gute Verschleißbeständigkeit bei linearer Belastung
- Haftzugfestigkeit bei Wolframkarbid und Chromkarbid > 70 MPa
- Werkstoffunabhängige Beschichtung
- Partielle Beschichtung möglich
- Hohe Dichtheit der Spritzschicht
- Sehr geringe Porosität (< 2%)
- Geringe metallurgische Veränderung
- Dünne Schichten mit hoher Maßgenauigkeit
Nachteile:
- Mikroporige Schichten
- Geringe punktuelle Belastbarkeit der Schicht
- Geringe Kanten- und Kerbschlagfestigkeit
- Reduzierter Korrosionsschutz
Schichtstärke: 0,1–0,3 mm
Temperaturbelastung: gering 100–300 °C
Bearbeitung: schleifen und läppen der Schichten möglich
Beim Laserauftragsschweißen wird der Laserstrahl über optische Komponenten auf die Bauteiloberfläche gelenkt, mittels einer Fokussierlinse in einem Brennfleck gebündelt und so der Grundwerkstoff erhitzt. Über eine koaxiale Schutzgas-Pulverdüse wird gleichzeitig der Pulverwerkstoff mit Trägergas / Schutzgas dem Prozess zugeführt und aufgeschmolzen. Dabei entsteht eine sehr gute Schichthaftung aufgrund der schmelzmetallurgischen Bindung an das Substrat.
Vorteile:
- Sehr geringer Wärmeeintrag in das Bauteil, daher minimaler Verzug und kleine Wärmeeinflusszone
- Keine aufwendige Nachbearbeitung des Bauteils nötig
- Sehr gute Schichthaftung aufgrund schmelzmetallurgischer Bindung (d.h. gezieltes Anschmelzen der Substratoberfläche aufgrund präzise steuerbaren Prozesses)
- Hohe Konturentreue komplizierter Werkstückformen
- Hoher Pulverwirkungsgrad > 70%, dadurch umweltschonende Technologie
- Partielle Beschichtung möglich
- Komplexe Geometrien möglich
- Hohe Kanten- und Kerbschlagbeständigkeit
- Gute Nachbearbeitungsmöglichkeit durch Drehen, Fräsen und Schleifen
Nachteil:
- Nur schweißbare Werkstoffe möglich
Schichtstärke: bis zu 2 mm Einzelschichtstärke, auch mehrlagig möglich
Schichthaftung: sehr gute Schichthaftung durch schmelzmetallurgische Bindung
Temperaturbelastung: gering 100–300 °C
Grundwerkstoff: schweißbare Stähle und Legierungen
Bearbeitung: drehen, schleifen, läppen der Schichten möglich
Anwendungen: Beschichtungen zur Verbesserung der Verschleiß-, Korrosions- und Temperaturbeständigkeit in Bereichen wie u.a. Armaturenbau, Bohr- und Drillingindustrie, Maschinenbau, Triebwerksbau etc. bei extremen Einsatzbedingungen (hoher Druck, lange Standzeit und extremer Verschleiß)
Ihr Nutzen
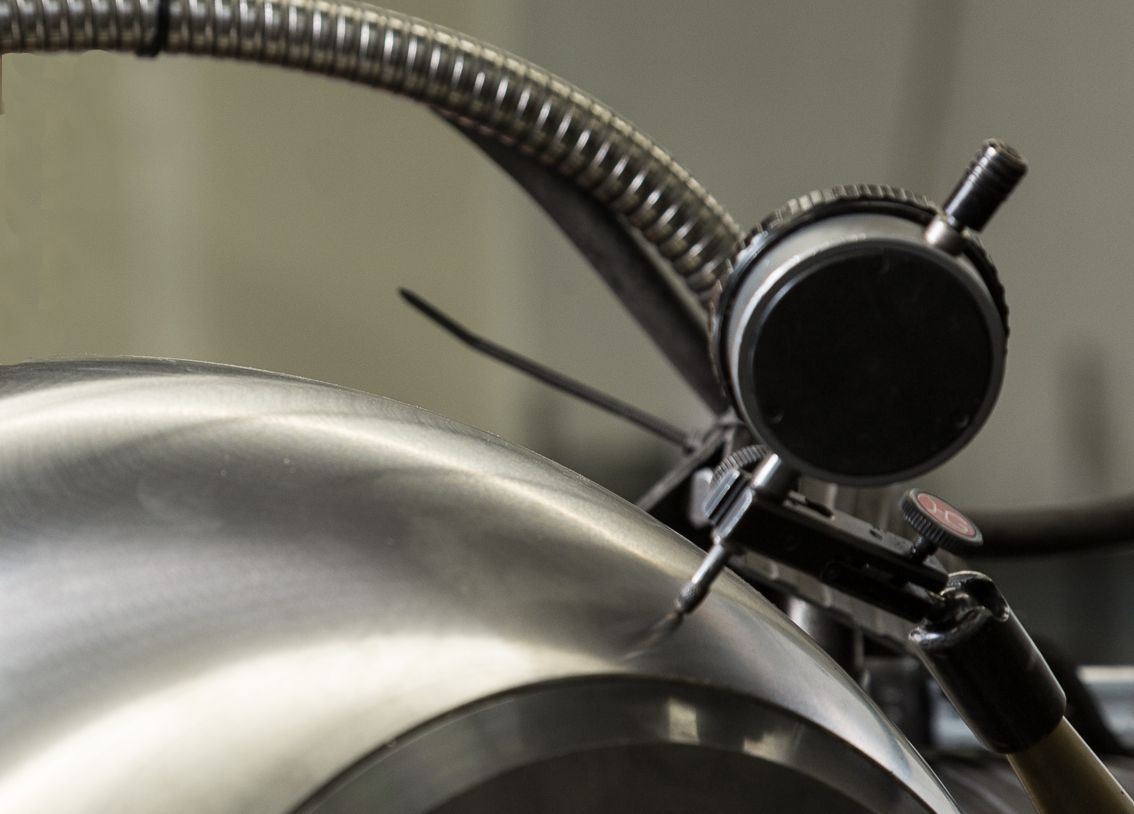
Was uns auszeichnet
Wann immer es um Abrasion, hohe Temperaturen, hohe Drücke, hohe Zyklenzahlen und hohe Strömungsge-
schwindigkeiten geht, sind wir mit absoluter Sicherheit der richtige Ansprechpartner für Sie.
Anwendungsbereiche
Armaturenindustrie
Metallisch dichtende Kugelhähne
Drilling
Verschleißminimierung für effiziente und wirtschaftliche Bohrungen
Maschinenbau
Maximierung von Standfestigkeit, Lebensdauer und Wirtschaftlichkeit
Downloads
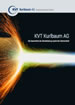
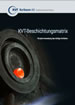