
KVT high-pressure valves
Designed to meet the most rigorous demands
Whenever abrasion, high temperatures, high pressure levels, large numbers of cycles and high flow velocities are critical factors, our valves are the option of choice.
We are especially proud of the high-pressure valves we have designed and developed for the gas industry.
We have put our experience with high-grade, durable materials and finishing techniques to excellent use, in particular to build a special program of regular valves. We also design and produce top-quality valves to meet your specific customized requirements.
- Areas of application for KVT valves:
- Gas dehydration plant
- Low-temperature separation (LTS) plant
- Cold frac plant
- Gas compressor stations
- Gas storage facilities
Our product portfolio
- Control valves
- Stop valves
- Check valves
- Gas volume control valves
Available variants: pressure levels ANSI 600 to ANSI 2,500 with nominal widths of 1" and 2", and API 10,000 with nominal widths of 1 13/16" to 4 1/16".
USPs for our valves:
KVT Kurlbaum AG satisfies the following approvals and standards:
- Acceptance of our valves is handled by accredited inspection organizations
- Declaration of compliance with the German Technical Code ("Technisches Regelwerk", TR) in collaboration with TÜV Nord
- European Pressure Equipment Directive (PED)
- EN 10 204, type 3.1
- Technical Code declaration
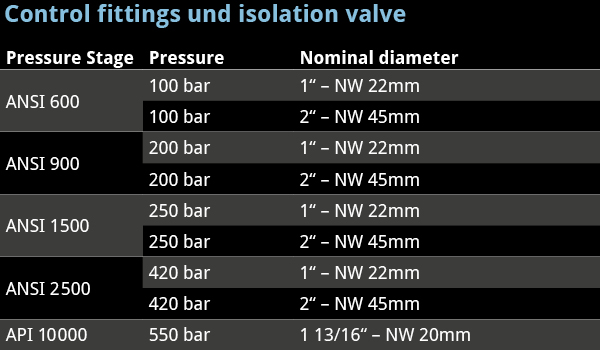
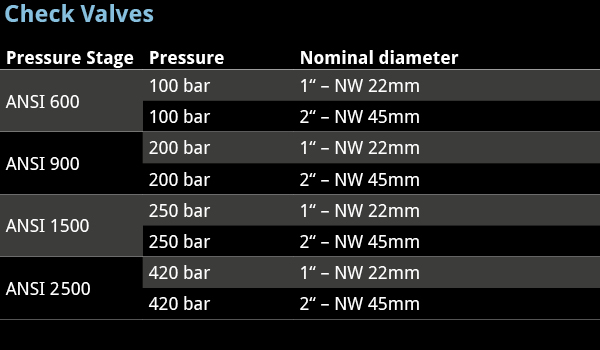
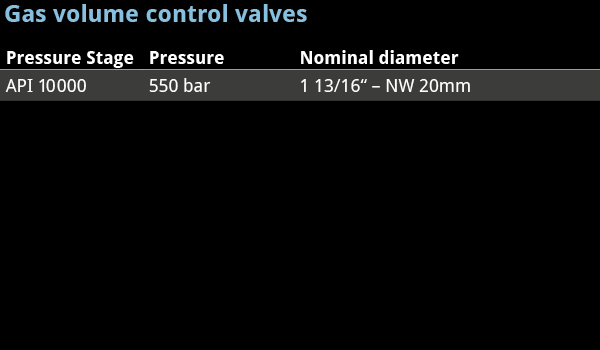
We only ever use wear-resistant parts. We never use cast parts. Our valve bodies and guiding systems are always manufactured from solid, high-grade materials to ensure compliance with both our customers' specifications and recognized standards.
This commitment enables us to satisfy the most rigorous pressure and temperature demands, thereby extending both service lives and servicing intervals.
We have channeled the experience we have gained in wear-resistance into developing and building valves specially for the gas industry. Interior fittings from KVT Kurlbaum for control and stop valves are always designed to a high quality.
Examples:
KVT balls and seats for control valves are made of carbide.
The plug stems in control valves are coated with a nickel-tungsten-carbide-based material.
The seats and shafts in stop valves have a nickel-tungsten-carbide coating.
These interior fittings thus shift wear, enabling significantly longer service lives and thus making plant more efficient.
Our valves are designed in such a way that they can, within the given dimensional constraints, be adjusted at any time to different conditions in the plant. This policy significantly reduces servicing costs and shortens delivery lead times.
In designing our gas volume control valves, we attached special importance to the interior fittings configuration. As a result, these fittings can be adjusted at any time in the flow coefficient range from Kv 10 to Kv 100 (Cv 11.56 to Cv 115.60).
The seats for KVT Kurlbaum valves are not welded to the valve bodies themselves. This facilitates substantial savings on maintenance, the procurement of spare parts and servicing times.
The benefits:
- Faster servicing
- Easier handling for local staff
- Low spare parts inventories
Our valves feature a large number of parts that are used in valves of all kinds. Around 20 percent of all fitted parts are built as assemblies, including stop, check and control valves. This too significantly improves delivery lead times.
In addition, we have factored the following customer requests into development of our valves:
- Simpler, faster servicing
- Lower inventory costs
- Long service lives
Our control valves are designed to operate with just about any drive system, leaving our customers free to choose their preferred system and vendor.